焊接规程
1 总则
1.1 凡属金属监督范围内的锅炉承压管道和部件的焊接工作,必须由考试合格并取得压力容器合格证的焊工担任。
1.2 严格按锅炉受热面承压部件焊接监察范围执行。
1.3 焊接焊条使用必需与母材的化学成份、机械性能、硬度值基本相对应。
1.4 用来直接与管子焊接的成型铸材(如阀门、三通),其含碳量不得超过0.25%。
1.5 焊接焊道无夹渣、气孔、咬边等缺陷,表面波纹均匀,内侧无凹陷、焊瘤等现象,焊口质量检验按要求分类评定。
1.6 本规范适用于碳素钢,普通低合金钢和耐热钢的手工电弧焊,氧-乙炔焊和钨极氩弧焊等焊接方法。
1.7 金属材料检验、设备焊口检查、通球试验、焊接评定、焊接头质量检验、焊接人员考核等项工作,应分别按有关规程进行。
1.8 焊接工作包括焊接、热处理和金属检查等,同时还必须遵守安全、环保、防火等规程的有关规定。
2 钢材与焊接材料
2.1 焊前必须查明所得材料的钢号,以便正确地选用相应的焊接材料和确定合适的焊接工艺和热处理工艺。
2.2 钢材必须符合国家标准(或部颁标准、专业技术条件),进口钢材必须符合该国国家标准或合同规定的技术条件。平顶山电厂常用钢材、常用国外钢材的化学成份、机械性能、硬度值,参考数据。详见表95。
2.3 属于锅炉监察范围内的锅炉受热面管及管道,使用异种规格和材料的管子代替时,应进行强度计算。
2.4 焊接材料[焊条、焊丝、钨棒、氩气、氧气、乙炔气(电石)和焊剂]的质量应符合国家标准(或有关标准)。
2.5 检修中使用取代材料时必须征得金属技术监督专职工程师的同意,并经总工程师批准(电力工业标准汇编《发电卷》之七)。
2.6 平顶山电厂常用电焊条的化学成分,机械性能及用途等参见表106,表107。
表 106 常用电焊条的化学成分、机械性能表
序
号 |
焊条
型号 |
统一
牌号 |
标准号 |
化学成分(%) |
机械性能 |
C |
Mn |
Si |
Cr |
Mo |
V |
Ni |
其
它 |
S |
P |
a
XMa |
s
% |
ak
j/cm2 |
不大于 |
1 |
J422 |
结422 |
GB981-76 |
≤
0.12 |
0.30-
0.60 |
≤
0.25 |
|
0.40-
0.70 |
|
|
|
0.035 |
0.050 |
412 |
18 |
78 |
2 |
J427 |
结427 |
0.50-
0.90 |
≤
0.50 |
|
0.40-
0.70 |
|
|
|
|
0.50 |
412 |
22 |
137 |
3 |
J507 |
结507 |
0.80-
1.40 |
≤
0.70 |
|
0.70-
1.00 |
|
|
|
|
0.035 |
588 |
18 |
98 |
表 106(续)
序
号 |
焊条
型号 |
统一
牌号 |
标准号 |
化学成分(%) |
机械性能 |
C |
Mn |
Si |
Cr |
Mo |
V |
Ni |
其
它 |
S |
P |
a
XMa |
s
% |
ak
j/cm2 |
不大于 |
4 |
R207 |
热207 |
GB982-78 |
≤
0.12 |
0.50-
0.80 |
≤
0.50 |
0.35-
0.65 |
0.90-
1.20 |
|
|
|
|
0.040 |
490 |
18 |
78 |
5 |
R307 |
热307 |
0.50-
0.90 |
≤
0.50 |
0.80-
1.20 |
|
0.10-
0.35 |
|
|
490 |
18 |
78 |
6 |
R317 |
热317 |
0.50-
0.90 |
≤
0.50 |
0.80-
1.20 |
|
0.10-
0.35 |
|
|
490 |
18 |
78 |
7 |
R337 |
热337 |
0.50-
0.90 |
≤
0.50 |
1.00-
1.40 |
|
0.10-
0.35 |
|
NbO.10
0.25 |
539 |
14 |
59 |
8 |
R407 |
热407 |
0.50-
0.90 |
≤
0.50 |
2.00-
2.50 |
|
|
|
|
539 |
14 |
59 |
表 107 常用电焊条的用途
类 别 |
统 一
牌 号 |
新 国 标 |
适用于焊接的钢材牌号 |
焊条性质及
电流极性 |
碳素钢焊条 |
J422 |
E4303 |
2、3、10、20、25、ZG15、ZG20、ZG25 |
酸性熔渣,
交流或直流 |
J427 |
E4315 |
2、3、10、20、25、ZG15、ZG20、ZG25 |
碱性熔渣,直流反极性 |
J507 |
E5015 |
2、3、10、20、25、ZG15、ZG20、ZG25、ZG35 |
同 上 |
钼钢焊条 |
R107 |
E5015-A1 |
15Mo3、16Mo |
同 上 |
铬钼钒钢焊条 |
R407 |
E6015-B3 |
10CrMo910 |
碱性熔渣,直流反极性 |
R317 |
E5515-B2V |
管壁温度510℃-540℃的12CrMoV、12CrMoV、15CrMoV、ZG15CrMo1V |
同 上 |
R337 |
E5515-B2VNb |
管壁温度540℃~570℃的10CrMo910、12CrMoV12Cr1MoV、ZG15CrMo1v |
同 上 |
2.7 特殊材料如生铁、不锈钢等常用焊条型号及适用范围,见表108。
表 108 特殊材料用焊条型号及适用范围
类 别 |
焊条型号 |
适用于焊接的钢材 |
焊条性质 |
电流极性 |
生铁焊条 |
Z308
Z408
Z508 |
薄件和加工面
球墨铁铸件
裂缝后砂眼 |
石墨型 |
交直流 |
堆焊条
|
D507 |
用于工作温度≤450 ℃的阀门制造
及轴类堆焊 |
低氢型 |
直流反接 |
D547Mo |
用于≤570 ℃阀门密面及其它 |
低氢型 |
直流反接 |
D802 |
用于高温高压阀门堆焊 |
钛钙型 |
交直流 |
不锈钢焊条 |
A132,A102 |
适用于奥氏体金属 |
钛钙型 |
交直流 |
2.8 平顶山电厂常用焊丝的化学成份和应用范围见表109和表110。
表 109 常用焊丝的化学成份和应用范围
钢号 |
标准号 |
牌 号 |
C |
Mn |
Si |
Cr |
Ni |
No |
S≤ |
P≤ |
碳
素
结
构
钢 |
YB199-63 |
H08 |
≤
0.10 |
0.30-
0.35 |
≤
0.03 |
≤
0.15 |
≤
0.30 |
|
0.04 |
0.04 |
YB199-63 |
H08A |
≤
0.10 |
0.30-
0.35 |
≤
0.03 |
≤
0.10 |
≤
0.25 |
|
0.03 |
0.03 |
YB199-63 |
H08Mn |
≤
0.10 |
0.30-
0.10 |
≤
0.03 |
≤
0.15 |
≤
0.30 |
|
0.04 |
0.04 |
YB199-63 |
H08MnA |
≤
0.10 |
0.30-
0.10 |
≤
0.03 |
≤
0.15 |
≤
0.25 |
|
0.03 |
0.03 |
YB199-63 |
H15 |
0.11-
0.18 |
0.30-
0.65 |
≤
0.03 |
≤
0.20 |
≤
0.30 |
|
0.04 |
0.04 |
YB199-63 |
H15 |
0.11-
0.18 |
0.80-
1.10 |
≤
0.03 |
≤
0.20 |
≤
0.30 |
|
0.04 |
0.04 |
低
合
金
钢 |
YB199-63 |
H12Mo |
≤
0.12 |
0.40-
0.70 |
0.15-
0.35 |
0.20 |
|
0.40-
0.60 |
0.03 |
0.03 |
YB199-63 |
H12MoCr |
≤
0.12 |
0.40-
0.70 |
0.15-
0.35 |
0.45-
0.65 |
≤
0.30 |
0.40-
0.60 |
0.03 |
0.03 |
YB199-63 |
H12CrMo
H08CrMoV |
≤
0.12 |
0.40-
0.70 |
0.15-
0.35 |
0.80-
1.50 |
≤
0.30 |
0.40-
0.60 |
0.03 |
0.03 |
表 110 常用焊丝的化学成份和应用范围
钢号 |
标准号 |
牌 号 |
使用范围 |
碳
素
结
构
钢 |
YB199-63 |
H08 |
施焊C2、C3、10、20钢管(工作压力>6MPa的锅炉受热面除外)及型钢 |
YB199-63 |
H08A |
同 上 |
YB199-63 |
H08Mn |
同 上 |
YB199-63 |
H08MnA |
施焊C2、C3、10、20钢管及其型钢 |
YB199-63 |
H15 |
施焊C2、C3、10、20钢管(工作压力>6 MPa的锅炉受热除外)及型钢 |
YB199-63 |
H15Mn |
同 上 |
低
合
金
钢 |
YB199-63 |
H12Mo |
施焊10、20、15Mo3、16Mo钢管 |
YB199-63 |
H12MoA |
施焊15Mo3、16Mo |
YB199-63 |
H08CrMoV |
施焊15Mo3、16Mo、12CrMo、13CrMo44、15CrMo钢管或介质温度≤510 ℃的12Cr1MoV、12CrMoV钢管 |
2.9 焊条丝的选用
根据母材的化学成份机械性能和焊接接头的抗裂性、碳扩散、焊接热处理以及使用条件等综合考虑。同种钢材焊接时,焊条焊丝的选用,一般应符合下列要求:
2.9.1 焊接材料金属性能和化学成份与母材相当。
2.9.2 工艺性能良好
2.10 钨极氩弧焊用的电极,宜采用铈钨棒,所用氩气纯度不得低于99.99%。
2.11 氧气-乙炔焊所用氧气纯度不低于98.5%,乙炔纯度应符合GB6891-86的规定(不低于96.5%)。
2.12 每批焊条应有经验的焊工进行工艺性能试验,用同种材料的管子吊焊、横焊口各一个,观察熔化过程,并作断口检查,焊条应满足下列要求。引弧容易,电弧燃烧稳定且无金属和熔渣的明显飞溅现象。药皮熔化均匀,无成片剥落。在焊缝形成过程中,溶渣能均匀地覆盖在金属表面,冷却熔渣易于除去。熔化金属内无裂纹,明显气孔和夹渣等缺陷。
2.13 焊条应放置在专库内,有专人保管,焊条挂牌并注明型号、批号、合格证明、工艺性能等,以防错用焊条。
2.14 低氢焊条在施工前必须进行烘干,烘干温度为300 ℃~400 ℃,保温时间为4小时左右。烘干后放在100 ℃左右的恒温箱内,随用随取。取出后放在焊条保温筒内,低氢焊条一般在常温下超过4小时即重新烘干,重复次数一般不超过三次。酸性焊条一般不烘干,但焊接重要构件时应经200 ℃~300 ℃烘干2小时左右。
3 焊前准备
3.1 管—管对口的准备及组合
3.1.1 管子焊口中心平面距联箱或汽包外壁、弯曲起点、支吊架外缘距离及两焊缝间允许值应符合表111。
表 111 两焊缝间允许值
名 称 |
示意简图 |
工作环境 |
允许值 |
焊缝中心平面距汽包、联箱外壁距离 |
|
工作压力≤6 MPa的锅炉受热面管 |
a≥50 mm
a≥D |
压力≥6 MPa的锅炉受热机管 |
a≥70 mm
a≥D |
焊缝中心平面距离弯曲起点距离 |
|
压力≤6 MPa的锅炉受热面管 |
a≥50 mm
a≥D |
管道 |
a≥150 mm |
焊缝中心平面距支吊架边缘距离 |
|
压力≤6 MPa的锅炉受热面管 |
a≥50 mm
a≥D |
压力≤6 MPa的锅炉受热面管 |
a≥70 mm
a≥D |
管道 |
a≥150 mm |
两焊缝中心平面间距离 |
|
受热面管及管道 |
a≥150 mm
a≥D |
3.1.2 管子的壁厚差和椭圆度应不超过国家技术标准的规定,管子对口时,其厚度差不得超过管壁厚的15%,最大不得超过3 mm,否则应按下图进行削薄。
管壁厚度不等的对口均匀削薄示意图151。
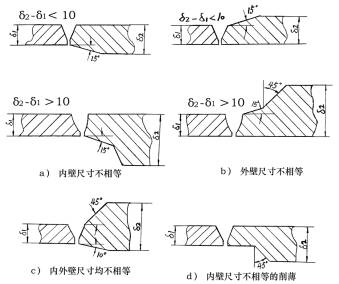
图 151 壁厚不等的对口均匀削薄示意图
3.1.3 焊口的位置应避开应力集中区且便于施焊及热处理,一般应符合下列要求:
3.1.3.1 锅炉受热面及管道焊口按表111进行。
3.1.3.2 管接头和仪表插座一般不可设置在焊缝或热影响区。
3.1.3.3 筒体的对接口其中心距离封头弯曲不小于壁厚加150 mm。
3.1.3.4 带有纵向焊缝的筒体和封头,相邻两纵向焊缝的距离应大于壁厚的3倍,且不小于150 mm。
3.1.3.5 焊接管的管孔应尽量避免开在焊缝上,并避免管孔焊缝与相邻焊缝的热影响区相重合,如必
须在焊缝上或其附近开孔时,应满足以下条件:
a) 管孔两侧大于孔径且不少于60 mm 范围内的焊缝应经无损探伤合格。
b) 孔边不在焊缝缺陷上。
3.1.3.6 搭接焊缝的搭接尺寸应不小于母材厚度的5倍,且不小于30 mm。
3.1.4 管子、管道、压力容器和钢结构的坡口形式应按设计图纸规定加工,如无规定时,坡口的型式和尺寸应按能保证焊接质量、填充金属量少,改善劳动条件,便于操作,减少焊接应力,适应探伤要求等原则选用。
3.1.5 焊件下料与坡口加工应按下列要求进行:
3.1.5.1 焊件坡口采用机械切削方法为宜,特别对大管径、合金钢钢管的汽水管道最为宜。
3.1.5.2 焊件坡口采用热加工(如气割),切口部分应先留有加工余量,以除去淬硬层及过热金属。
3.1.6 焊件经下料及坡口加工,应按下列要求进行检查,合格后方可进行组对。
3.1.6.1 淬硬性较大的钢材如使用火焊(嘴)割下料坡口,加工后要经表面探伤合格。
3.1.6.2 坡口处母线无裂纹、重皮、坡口损伤及毛刺等缺陷。
3.1.6.3 坡口加工尺寸符合图样要求。
3.1.6.4 按有关条例规定的清理范围内无裂纹,夹层等缺陷。
3.1.7 焊件在组装前应将焊口内外表面及附近母材外壁的油漆、垢、锈等清理干净,直到发出表面金属光泽,清理范围规定如下:
3.1.7.1 弧焊对接焊口,每侧各为15 mm左右。
3.1.7.2 角接接头焊口,焊脚值为壁厚加10 mm。
3.1.8 焊件对口时一般应做到内壁齐平,如有错口,其错口值应符合下列要求:
3.1.8.1 对接单面焊的局部错口值不应超过壁厚的10 %且不大于1 mm。
3.1.8.2 对接双面焊的局部错口值不应超过壁厚度的10%,且不大于3 mm。
3.1.9 不同厚度焊件对口时,其厚度差可按下列方法处理:
3.1.9.1 内壁尺寸不相等外壁齐平时,其厚度可加工成图151(a)的形式。
3.1.9.2 外壁尺寸均不相等而内壁齐平时,可加工成图151(b)的形式。
3.1.9.3 内外壁尺寸不相等,厚度差≤5 mm时,在不影响焊件强度的条件下,可加工成图151(d)的形式。
3.1.10 焊口的局部的间隙过大时,应设法修至规定尺寸,严禁在间隙内加填塞物(如钢筋等)。
3.1.11 焊件组合焊接时应注意事项
3.1.11.1 焊接组装时应垫置牢固,不可晃动或搬动,以防止在焊接和热处理过程中产生变形和附加应力。
3.1.11.2 除设计规定的冷焊口外,其余焊口应禁止用强制对口,且不允许利用热膨胀法对口,以防附加应力。
3.1.11.3 焊接件内应无风、水、汽等流动介质。
3.1.11.4 整体施焊工作包括对口装配、施焊、热处理和检查等工序,每项工序次序符合要求后方准进行下道工序施工。
3.1.12 焊材的选择及烘干,碱性焊条,焊前经过300 ℃~400 ℃烘干4 h左右;酸性焊条则在200 ℃~300 ℃烘干2 h左右。
3.1.13 装配与定位焊装配定位焊所用焊条与正式焊接所使用的焊条相同,按园周方向均布,大管子可焊2~3处,小管子焊1~2处,每处定位焊缝长10 mm左右,装配管子时应预留间隙(一般应为焊条直径),并保证同心度(小于或等于壁厚的10%。且≤1 mm)。
3.2 板一管对口的准备及组合
3.2.1 如图152,管一板“骑座”式组合对口要求。
3.2.1.1 管孔离板缘应大于50 mm。
3.2.1.2 当钢板厚度δ≤10 mm时,钢板需加刚性固定,当钢板厚度δ>10 mm时,钢板不需加刚性固定。
3.2.1.3 管板件的焊缝凸度或凹度应不大于1.5 mm,其焊脚为壁厚加3 mm~6 mm。
3.2.1.4 单面焊的板状件和外径大于或等于Φ133 的管状件背面焊接缝余高应不大于3 mm,外径≥Φ60 mm,管状件背面焊缝余高应≤2 mm。
3.2.1.5 焊缝宽度比坡口每侧增宽≤2 mm~4 mm,且宽度差≤2 mm。
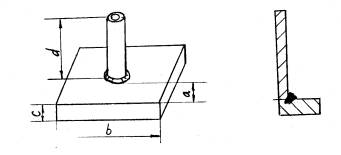
图 152 管一板焊接试样示意图
3.2.2 焊材的选择及烘干。碱性焊条,焊前经300 ℃~400 ℃,烘干4h,酸性焊条则经200 ℃~300 ℃烘干2 h。
3.2.3 焊前清理 必须将指定范围内的油、锈及其他污物清理干净,直至露出金属光泽为止。
3.2.4 定位焊通常都是三处,按圆周方向均匀分布。
3.2.5 定位焊也可只焊两点,第三点处作为引弧开始的位置。
3.2.6 必须按正式焊接的要求焊定位焊缝,定位焊缝不能太高,每段长度在10 mm左右,且要保证管子轴线垂直孔板。
4 管—管对口焊接
4.1 垂直固定小径管对接
4.1.1 装配与定位焊装配要求,见表112。
表 112 装配与定位焊装置要求
坡口角度
° |
装配间隙
mm |
钝边
mm |
错边量
mm |
60~70 |
前2.5 后3.2 |
0~1 |
≤1 |
定位焊必须采用正式焊时的焊条焊接。
4.1.2 焊接及操作工艺要点
由于管径小,管壁薄,焊接过程中温度上升较快,熔池温度容易过高,因此,打底焊采用断弧焊法进行施焊,断弧焊打底,要求将熔滴给送要均匀,位置要准确,熄弧和再引弧时间要灵活、果断。
4.1.2.1 焊道分布
两层三道如图153。
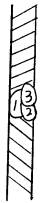
图153 小管径横焊焊道分布
4.1.2.2 焊接工艺参数的选择,见表112。
表 112
焊接层次 |
焊条直径
mm |
焊接电流
A |
打底焊 |
2.5 |
60~80 |
盖面焊 |
70~90 |
4.1.2.3 打底焊
其关键是保证焊透,工件不能被击穿,不能产生焊瘤,不能出现内凹。
a) 打底层施焊时,焊条与工件的角度如图154,起弧时采用划擦法将电弧在坡口内引燃,等看到坡口两侧金属局部熔化时,焊条向坡口根部压送熔化并击穿坡口根部,将熔滴送至坡口背面,此时听见背面电弧的穿透声,这时便形成了第一个熔池,第一个熔池形成后,即将焊条向焊接的反方向作划挑动作迅速灭弧,使熔池降温,待熔池变暗时,在距离熔池前沿约5 mm左右的位置重新将电弧引燃、压低电弧向背面压,并稍作停顿,同时即听见电弧击穿的声音,这时便形成了第二个熔池,熔池形成后,立即灭弧。如此反复,均匀的采用这种一点击穿法向前施焊。
b) 熔池形成后,熔池的前沿应能看到熔孔,使上坡口面熔化掉1.0 mm~1.5 mm,下坡口面略小,施焊时,要注意把握住三个要领:即一“看”、二“听”、三“准”。“看”就是要注意观察熔池形状和熔孔大小,使熔池形状基本一致,熔孔大小均匀。并要保持熔池清晰、明亮、熔池和铁水要分清。“听”是听清电弧击穿焊件根部的“噗”、“噗”声。“准”是要求每次引弧的位置与焊至熔池前沿的位置准确,既不能超前,又不能拖后,后一个熔池搭接前一个熔池的2/3左右。
c) 更换焊条收弧时,将焊条继续向熔池后方点2下~3下,缓降熔池的温度,将收弧形成的缩孔消除或带到焊缝表面,以便在下一根焊条进行焊接时将其熔化掉。
d) 打底层焊缝的接头方法,可采用热接和冷接法。
热接法是更换焊条的速度要快,在前一根焊条焊完收弧,熔池尚未冷下来,呈红热状态时,立即在熔池前面5 mm~10 mm的地方将电弧引燃,退至收弧后沿,焊条向坡口根部压送,并稍停顿,当看见电弧击穿试件根部的声音时,即可熄弧然后进行焊接。
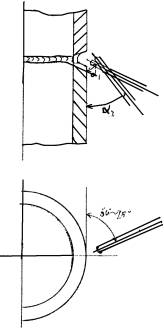
图154 打底焊时焊条角度 图155 盖面时的焊条角度
(α1=70°~80°α2=60°~70°)
冷焊法是在施焊前,先将收弧处焊道打磨成缓坡状,然后按热接法的引弧及操作方法进行焊接。
焊接封闭接头时,先将焊缝端部打磨成缓坡形,然后再焊,焊到缓坡前沿时,电弧向坡口根部压送,并稍作停顿,然后焊过缓坡,直至超过正式焊缝约5 mm~10 mm填满弧坑熄弧。
4.1.2.4 盖面焊
保证表面平整,尺寸合格。
a) 焊前,将上层焊缝的熔渣及飞溅物清理干净,将焊缝接头处打磨平整。然后进行焊接。盖面层分上、下两道进行焊接,焊接时由上至下进行施焊,焊条与工件的角度如图155所示。
b) 盖面层焊接时,运条要均匀采用较短电弧,焊下面的焊道时,电弧应对准填充焊道的下沿,略横向摆动,使熔池下沿稍超出坡口下棱边(≤2 mm),应使熔化金属覆盖住打底焊道的1/2~2/3,为焊上面的盖面焊道的防止咬边和铁水下淌现象,要适当增大焊接速度或减少焊接电流,调整焊条角度,以保证整个焊缝外表均匀、整齐、美观。
4.2 水平固定小径管对接
4.2.1 装配与定位焊装配要求,见表113。
表 113 装配与定位焊装配要求
坡口角度
0 |
装配间隙
mm |
钝边
mm |
错边量
mm |
60~70 |
0点处3.2,6点处2.5 |
0~1 |
≤1 |
定位焊必须采用正式焊时的焊条焊接。
由于管径小,管壁薄,焊接过程温度上升较快,焊道温度容易过高。打底焊不宜用连弧焊法,而采用断弧焊的方法。
4.2.2.1 焊道分布两层两道
4.2.2.2 焊接工艺参数的选择,见表114。
表 114 焊接工艺参数
焊接层次 |
焊条直径
mm |
焊接电流
A |
打底焊 |
2.5 |
60~80 |
盖面焊 |
70~90 |
4.2.2.3 打底焊(为叙述方便,假定沿垂直中心线将管子分成前后两个半周,如图156所示)。
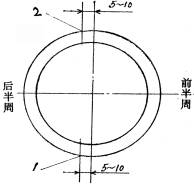
图 156 前半周焊缝引弧与收弧位置
(1-引弧处;2-收处)
a) 焊前半周时,引弧和收弧部位要超过中心线5 mm ~10 mm。
b) 焊接从仰焊位置开始,起焊时采用划擦法在坡口内引弧待形成局部焊缝,并看到坡口两侧金属即将熔化时,焊条向坡口根部压送,弧柱透过内壁的1/2,熔化并击穿坡口的根部,此时可听到背面电弧的击穿声,并形成第一个熔池,第一个熔池形成后,立即将焊条抬起熄弧,使熔池降温,待熔池变暗时,重新引弧并压低电弧向上给送。形成第二个熔池,均匀地点射给熔滴,向前施焊,如此反复。
c) 焊接仰焊位置时,焊条应向上顶送得深些,电弧尽量压低,防止产生内凹、未熔合、夹渣等缺陷。
d) 焊接立焊及平焊位置时,焊条向坡口里面的压送深度应比仰焊浅些,弧柱透过内壁1/3熔透根部钝边,防止因温度过高,液态金属在重力作用下,造成背面焊缝超高,或产生焊瘤、气孔等缺陷。
e) 收弧方法,当焊完一根焊条收弧时,应使焊条向管壁左或右侧回拉带弧约10 mm,或沿着熔池向后稍快点焊2点~3点下,以防止突然熄弧造成弧坑处产生缩孔、裂纹等缺陷。同时也能使收尾处形成缓坡,有利于下一根焊条的接头。
f ) 在更换焊条进行焊缝中间接头时,有热接和冷接两种方法。
热接法更换焊条要迅速,在前一根焊条的熔池没有完全冷却时,呈红热状,在熔池前面约5 mm~10 mm处引弧,待电弧稳定燃烧后,即将焊条施焊至熔孔,将焊条稍向坡口里压送,当听到击穿声时即可断弧,然后按前面介绍的焊法继续向前施焊。
冷接法在施焊前,先将收弧处焊道打磨成缓坡状,然后按热接法的引弧及操作方法进行焊接。
g) 后半周下接头仰焊位置的焊接,在后半周焊缝施焊前,先将前半周焊缝起头处打磨成缓坡状,然后在坡前面约5 mm ~10 mm处引弧,预热施焊,焊至缓坡末端时将焊条向上顶送,待听到击穿声,根部熔透形成熔孔后,正常向前施焊,其它位置焊法均同前半周。
h) 后半周水平位置上接头的施焊,在后半周焊缝施焊前先把前半周焊缝收尾熄弧处打磨成缓坡,当焊至后半周焊缝与前半周焊缝接头封闭处时,将电弧略向坡口里压送并稍停顿,待根部焊透,焊过前半周焊缝的10 mm,填满弧坑后再熄弧。
i ) 施焊过程中经过定位焊缝时,将电弧稍向里压送以较快的速度经过定位焊缝,过渡到前方坡口处进行正常施焊。
4.2.2.4 盖面焊
要求焊缝外形美观、无缺陷,盖面层焊接施焊前,应将前层的熔渣和飞溅清除干净,焊缝接头处打磨平整,前半周焊缝起头和收尾部位,都要超过管子的中心线5 mm ~10 mm,采用锯齿形或月牙形运条方法连续施焊,但横向摆动的幅度要小,在坡口两侧略做停顿稳弧,防止产生咬边,在焊接过程中,要严格控制弧长,保持短弧施焊以保证焊缝质量。
4.3 垂直固定大径管对接
4.3.1 装配与定位焊装配要求,见表115。
表 115 装配与定位焊装配要求
坡口角度
0 |
装配间隙
mm |
钝边
mm |
错边量
mm |
60~70 |
前2.5,后3.2 |
0-1 |
≤1 |
定位焊必须采用正式焊时的焊条焊接。
4.3.2 焊接及操作工艺要点
管子由于有弧度,焊接电弧应沿大管子圆周均匀移动。
4.3.2.1 焊道分布:四层七道,见图157。
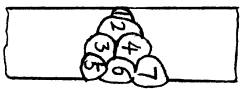
图 157 大径管横焊焊道分布
4.3.2.2 焊接工艺参数的选择,见表116。
表 116 焊接工艺参数
焊接层次 |
焊条直径
mm |
焊接电流
A |
打底焊 |
2.5 |
70~90 |
填充焊 |
3.2 |
110~130 |
盖面焊 |
105~125 |
4.3.2.3 打底焊
要求焊透并保证背面焊道成形美观,无缺陷。
a) 大管径打底层焊条角度,如图158所示。
图 158 大径管打底层焊条角度
b) 打底层在管子的上坡口上引燃电弧,然后向管子的下坡口移动,等坡口两侧熔合后,焊条向坡口里压,同时稍作停顿,这时可以看到管子坡口根部已被熔化并被击穿,形成熔孔。此时焊条上、下摆动,作锯齿形运条连续向右施焊。
c) 打底层施焊时,为得到优质的焊缝和良好的背面焊缝成形,焊接电弧要控制短些,焊条摆动向前移动的间距不宜过大,焊至坡口两侧停留时,要注意在上坡口的停留时间比在下坡口停留的时间稍长。焊接电弧的1/3保持在熔池前,用来熔化和击穿坡口根部,电弧的2/3覆盖在熔池上,并保持熔池的形状大小基本一致。
d) 在焊接过程中,还要控制熔孔的大小,使上坡口面熔化掉约1.0 mm~1.5 mm,下坡口略小些。施焊时若发现下坡口出现较大的熔孔时,工件焊缝背面易产生下坠或焊瘤。当焊条即将焊完,需要更换焊条收弧时,要将焊条向焊接的反方向接回约10 mm~15 mm,使电弧拉长,直到熄灭。这样可以把收弧缩孔消除或带到焊道表面,以便在下一根焊条进行焊接时,将其熔化掉。
e) 打底层焊缝的接头方法可采用热接和冷接法。
热接法要求更换焊条的速度要快,在熔池尚未冷却之前,呈红热状态时,立即在熔池后面约10 mm处引燃电弧,焊条作上下摆动向前施焊至收弧的前沿时,将焊条向坡口根部压送,并稍作停顿。然后将焊条渐渐抬起至正常焊接的位置,并向前施焊。采用冷接法时,先将收弧处焊道打磨成缓坡状,然后按热接法的引弧及操作方法进行焊接。
f ) 工件的打底层即将焊完,需要进行接头封闭时,应事先将始焊处的焊缝端部打磨成缓坡形,然后再施焊,焊至缓坡处前端,焊条向坡口里压,并稍作停顿然后继续向前焊过缓坡约10 mm,待填满弧坑后,即可熄弧。
4.3.2.4 填充焊
保证坡口两侧熔合好,焊道表面平整。
a) 填充层施焊前,将前一层的熔渣及飞溅物清理干净,并将打底层焊缝接头处打磨平整,再进行填充焊接。填充层为上、下两道焊缝进行焊接,焊接时由下至上施焊。焊条与工件的角度如图159。
b) 下道填充层焊接时,应注意观察下坡口及封底层焊缝与管子的下坡口之间的夹角处熔化情况,焊上一道焊缝时,要注意封底层焊缝与管子上坡口之间夹角处的熔化情况。同时上道焊缝应覆盖住下道焊缝的1/3~1/2,避免填充层焊缝的表面出现凹槽或凸起.填充层焊完后,下坡口应留出约2 mm,上坡口应留出约0.5 mm,坡口两侧的边缘棱边不要破坏,以便盖面。
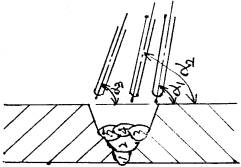
图 159 大径管填充焊时的焊条角度 图 160 盖面时的焊条角度
α1=90°~100°,α2=60°~70° α1=75°~85°,α2=70°~80°,α3=60°~70°
4.3.2.4 盖面焊盖面层分三道或以上,施焊时,焊条与焊件的角度如图10¥所示。
4.4 水平固定大径管对接
4.4.1 装配与定位焊装配要求,见表117。
表 117 装配与定位焊装配要求
坡口角度
0 |
装配间隙
mm |
钝边
mm |
错边量
mm |
60~70 |
0点处3.2 6点处2.5 |
0~1 |
≤1 |
定位焊:大管子水平吊口,接口在垂直面内“0”点处。
4.4.2 焊接及操作工艺要点
4.4.2.1 焊道分布:四层四道。
4.4.2.2 焊接工艺参数的选择,见表118。
表 118 焊接工艺参数
焊接层次 |
焊条直径
mm |
焊接电流
A |
打底焊 |
2.5 |
70~90 |
填充焊 |
3.2 |
110~130 |
盖面焊 |
3.2 |
100~120 |
4.4.2.3 打底焊要求根部焊透且成形美观。
a) 底层焊缝的焊接,沿垂直中心线将管分为半周,称前半周和后半周,各分别进行焊接,仰焊—平焊。在焊前半周焊缝时,在仰焊位置的起焊点和平焊位置的终点焊都必须超过工件的半周(超过中心线约5 mm~10 mm),如图161所示。
b) 半周从仰焊位置开始,在1点处引燃电弧后将焊条送到坡口根部的一侧预热施焊,并形成局部焊缝,然后将焊条向另一侧坡口进行搭焊,待连上后将焊条向上顶焊,当坡口根部边缘熔化形成熔孔后,压低电弧作锯齿形向上连续施焊。横向摆动到坡口两侧时稍作停顿,以保证焊缝与母材根部熔合良好。
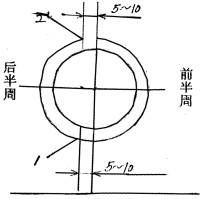
1-起点 2终点
图 161 前半周焊缝的起点和终点
c) 焊位置时,易产生内凹、未焊透和夹渣等缺陷。因此焊接时,焊条应向上顶送深些,尽量压低电弧,弧柱透过内壁约1/2,熔化坡口根部边缘两侧形成熔孔。焊条横向摆动幅度较小,向上运条速度要均匀,不宜过大,并且要随时调整焊条角度,防止熔池金属下坠而造成焊缝背面产生内凹和正面焊缝出现焊瘤。
d) 焊接立焊位置时,焊条向坡口内的给送应比仰焊浅些。
e) 焊接平焊位置时,焊条向坡口内的给送应比立焊再浅些,弧柱透过内壁约1/4,熔化坡口根部边缘的两侧,以防止背面焊缝过高或产生焊瘤、气孔等缺陷。
f ) 更换焊条进行焊缝中间接头时,采用热接法或冷接法均可。
g) 后半周焊缝下接头仰焊位置的施焊:在后半周焊缝施焊前,先将前半周焊缝起焊处易产生的气孔、未焊透等缺陷清除掉,然后打磨成缓坡形。施焊时在前半周焊缝前约10 mm处引弧,然后退至缓坡末端时将焊条向上顶送,待听到击穿声根部熔透形成熔孔时,即可正常运条向前施焊。其它位置焊法均同前半周。
h) 焊缝上接头水平位置的施焊:在后半周焊缝施焊前,应将前半周焊缝在水平位置的收弧打磨成缓坡形,当后半周焊缝与前半周焊接头封闭时,要将电弧稍向坡口内压送,并稍作停顿,待根部熔透超过前半周焊缝约10 mm,填满弧坑后再熄弧。
i ) 在整周焊缝焊接过程中,经过正式定位焊缝时,只要将电弧稍向坡口内压送,以较快的速度通过定位焊接处,过渡到前方坡口处进行正常施焊即可。
4.4.2.4 填充焊要求坡口两侧溶合好,填充焊道表面平整。
a) 填充焊施焊前应将打底层的熔渣、飞溅物清理干净,并将焊缝接头的处的焊瘤等打磨平整,施焊时的焊条角度与打底层相同,采用锯齿形运条方法,焊条摆动的幅度较打底层宽,电弧要控制短些,两侧稍作停顿稳弧,但焊接时应注意不能损坏坡口边缘的棱边。
b) 仰焊位置运条速度中间要稍快,形成中间较薄的凹形焊缝。
c) 立焊位置运条采用上凸的月牙形摆动,防止焊缝金属下坠。
d) 平焊仍改用锯齿形运条,使填充焊道表面平整或稍凸起。
e) 填充层焊完后的焊道,应比坡口边缘稍低1.0 mm~1.5 mm,保持坡口边缘的原始状态,以便在盖面层施焊时能看清坡口边缘,以保证盖面层的焊缝齐、直。
f ) 填充层焊缝中间接头,更换焊条要迅速,在弧坑上方约10 mm处引弧,然后把焊条拉到弧坑处,按弧坑的形状将它填满,然后正常焊接,进行中间接头时,切不可直接在焊缝接头处直接引弧施焊,这样易使焊条端部的裸露焊芯在引弧时,因无药皮的保护而产生的密集气孔留在焊缝中,而影响焊缝的质量。
4.4.2.4 盖面焊要求保证焊缝尺寸,外形美观,熔合好,无缺陷。
a) 盖面层施焊前应将填充层的焊渣和飞溅物清理干净,清除后施焊时的焊条角度与运条方法均同填充层,但焊条水平横向摆动的幅度应比填充层更宽,当摆至坡口两侧时,电弧应进一步缩短,并要稍作停顿,以避免咬边。从一侧摆至另一侧时应稍快一些,以防止熔池金属下附而产生焊瘤。
b)处理好盖面层焊缝中间接头是焊好盖面层焊缝的重要环节。当接头位置偏下时,接头处过高;偏上时,则造成焊缝脱节。焊缝接头方法同填充层。
4.5 焊后热处理
热处理是为了降低焊接接头的残余应力,改善焊缝金属的组织与性能。热处理过程应严格按照本规程及有关规定进行。
下列焊接接头焊后必须进行热处理:
4.5.1 δ>30 mm碳素钢管子与管件。
4.5.2 δ>32 mm碳素钢容器。
4.5.3 δ>28 mm的普通低合金钢容器。
4.5.4 δ>10 mm或φ>108 mm的15CrMo,12Cr2Mo管子。
4.5.5 δ>8 mm或φ>108 mm的12Cr1MoV或12CrMoV管子。
4.5.6 δ>6 mm或φ>63 mm的12Cr2MoWVB管子。
4.5.7 经焊接工艺评定需要做热处理的焊件。
4.6 焊后检验
4.6.1 外观检验
4.6.1.1 外观检验是用眼睛或放大倍数在5倍左右的放大镜,检查焊缝正面和背面的缺陷性质和数量,并用测量工具测定缺陷位置和尺寸。
4.6.1.2 焊缝外观必须符合以下条件:
a) 焊缝表面应是原始状态,焊缝表面没有加工或补焊痕迹。
b) 焊缝表面不得有裂纹、未熔合、气孔、夹渣和焊瘤等缺陷。未焊透和背面凹坑不得超过表119的规定。
c) 管子的错边量<10%,且≤1 mm。
d) 焊缝外形尺寸符合表110。
e) 外径小于等于60 mm的管子要作通球试验。外管大于或等于32 mm时,通球直径为管内径的85%;管外径小于32 mm时,通球直径为管内径的75%。
表 119 未焊透和背面凹坑允许的最大尺寸
缺陷名称 |
允许的最大尺寸 |
咬边 |
深度<0.5 mm,两侧咬边总长<20%的管子外周长 |
未焊透 |
深度<δ15%,且<1.5 mm;总长<10%,管子外周长 |
背面凹坑 |
当δ<6 mm时,深度<δ25%,且<1 mm;当δ<6 mm时,深度<δ20%,且<2 mm;
仰焊部位不计,总长不超过管子外周长的10% |
表 120
焊缝余高 |
焊缝余高差 |
焊缝宽度 |
平焊位置 |
其它位置 |
平焊位置 |
其它位置 |
比坡口每侧增宽 |
宽度差 |
0 mm~3 mm |
0 mm ~4 mm |
<2 mm |
<3 mm |
0.5 mm ~2.5 mm |
<3 mm |
4.6.2 无损探伤质量标准见表121。
表 121 无损探伤质量标准
焊缝类别 |
Ⅰ |
Ⅱ |
Ⅲ |
|
厚度
mm |
<6 |
>6 |
<6 |
>6 |
<6 |
>6 |
|
缺
陷
名
称
|
裂纹、未熔合 |
不允许 |
|
|
根
部
未
焊
透 |
双面焊 |
|
单面焊 |
不允许 |
深度≯10%δ,且≯1.5 mm,累计长度≯焊缝长度的10% |
深度≯15%δ,且≯2 mm累计长度≯焊缝长度的15% |
|
内凹(塌腰) |
深度≯20%δ,且≯2 mm |
深度≯15%且δ≯1.5 mm |
深度≯25%δ,且≯2 mm |
深度≯25%δ,且≯2 mm |
深度≯30%δ,且≯2 mm |
深度≯25%且≯2.5 mm |
|
单
个
气
孔 |
径向 |
≯25%δ |
25%δ且≯3 mm |
≯25%δ |
≯25%δ,且≯4 mm |
≯25%δ |
≯25%δ,且≯4 mm |
|
轴、周向 |
≯2 mmδ |
30%δ且≯5 mm |
≯2 mmδ |
≯30%δ,且≯6 mm |
≯3 mmδ |
≯30%δ,且≯7 mm |
|
|
|
|
|
|
|
|
|
|
|
|
表 121(续)
焊缝类别 |
Ⅰ |
Ⅱ |
Ⅲ |
|
厚度
mm |
<6 |
>6 |
<6 |
>6 |
<6 |
>6 |
|
缺
陷
名
称
|
单
个
夹
渣 |
径向 |
≯25%δ |
20%δ且≯3 mm |
≯25%δ |
≯20%δ,且≯4 mm |
≯25%δ |
≯20%δ,且≯4 mm |
轴、周向 |
≯30%δ |
25%δ且≯4 mm |
≯30%δ |
≯25%δ,且≯4 mm |
≯30%δ |
≯30%δ,且≯5 mm |
密集气孔
和夹渣 |
不允许 |
1 每1cm2面积内有直径<0.8 mm气孔或夹渣的超过5个,或总面积不超过3cm2
2 沿圆周(或长度)方向10倍厚度的范围内,气孔和夹渣的累计长度不超过壁厚相邻缺陷间距离,如超过最大缺陷长度5倍时,则按单个论。 |
沿厚度方向同一直线上,各种缺陷的总和 |
≯25%δ且≯1.5 mm |
≯25δ,且
≯3 mm |
≯25δ,且
≯1.5 mm |
≯25%δ,且
≯4 mm |
≯26%δ,且≯2 mm |
≯30%δ,且≯5 mm |
|
|
|
|
|
|
|
|
|
|
|
5 插座焊接
5.1 垂直固定俯焊
5.1.1 装配与定位焊
5.1.1.1 装配定位焊所用焊条与正式焊接时的焊条相同。
5.1.1.2 定位焊缝可采用点固一点或二点两种方法。每一点的定位焊缝长度约10 mm,且保证工件之间同心,无错边。
5.1.1.3 采用正式定位焊缝,要求背面成形无缺陷,定位焊是打底焊的一部分。焊前将定位处的两端打磨成缓坡形。
5.1.1.4 装配要求,见表122。
表 122 装配要求
坡口角度
0 |
装配间隙
mm |
错边
mm |
错边量
mm |
45±5 |
2.5~3.5 |
0~1 |
<1 |
5.1.2 焊接及操作工艺要点
5.1.2.1 焊道分布
三层四道,垂直固定俯焊焊道分布如图162。

图162 垂直固定俯焊焊道分布
5.1.2.2 焊接工艺参数见表123。
表 123 焊接工艺参数
焊接层数 |
焊条直径
mm |
焊接电流
A |
打底焊 |
2.5 |
60~80 |
填充焊 |
3.2 |
110~130 |
盖面焊 |
3.2 |
100~120 |
5.1.2.3 打底焊:保证根部焊透,防止烧穿和产生焊瘤,俯焊打底焊的焊条角度,如图163所示。
a) 在左侧定位焊缝上引弧,稍预热后向右移动焊条,当电弧到达定位焊缝前端时,往前送焊条,待形成熔孔后,稍向后退焊条,保持短弧,并开始小幅度锯齿形摆动,电弧在坡口两侧稍停留,进行正常焊接。
b) 焊接时电弧要短,焊接速度不宜过大,电弧在坡口根部稍停留,焊接电弧的1/3保持在焊孔处,2/3覆盖在熔池上,同时,要保持熔孔的大小基本一致,避免根部产生未熔合、未焊透、背面焊道太高、烧穿或焊瘤等缺陷。
c) 焊接过程中应根据实际位置,不断地转动手臂和手腕,使熔池与管子坡口面连在一起并保持均匀的速度运动,待焊条快熔化完时,电弧迅速向后拉直至灭弧,使弧坑处显斜面。
d) 焊缝接头有两种接法,热接和冷接法(详参见《管-管焊接及操作工艺》部分)。
e) 焊封闭焊缝接头时,先将接缝端部打磨成缓坡形,待焊到缓坡前沿时,焊条伸向弧坑内,稍作停顿,然后向前施焊并超过缓坡与焊缝重叠约10 mm,填满弧坑后熄弧。
5.1.2.4 填充焊:填充焊必须保证坡口两边熔合好,其焊条角度以如图164所示。
a) 焊填充层前,先清理打底层焊道上的熔渣,将焊道局部凸起处磨平。然后按打底焊相同的步骤焊接。
b) 焊填充层施焊时采用短弧焊,可一层填满,注意上、下两侧的熔化情况,保证温度均衡,使坡口处熔合良好,填充层焊缝要平整,不能凸出过高,焊缝不能过宽,为盖面层后施焊打好基础。
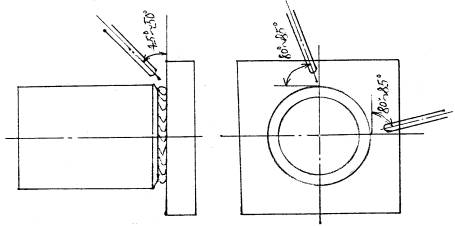
图163 俯焊打底时的焊条角度

图164 填充时的焊条角度 图165 盖面时的焊条角度
5.1.2.5 盖面焊:盖面焊必须保证管子不咬边和焊脚对称,其焊条角度如图165所示。
a) 盖面焊前先清理填充层焊道上的焊渣,并将局部凸起处磨平。
b) 焊接时要保证熔合良好,掌握好两道焊道的位置,避免形成凹槽或凸起,第4条焊道应覆盖第三条焊道上面的1/2或2/3。必要时还可以在上面用φ2.5焊条再盖一道,以免咬边。
5.2 水平固定全方位焊
5.2.1 装配与定位焊装配要求,见表124。
表 124 装配与定位焊装配要求
坡口角度
0 |
装配间隙
mm |
错边
mm |
错边量
mm |
45±5 |
6点处2.5,0点处3.2 |
0~1 |
<1 |
5.2.2 焊接及操作工艺要点
水平固定焊接,包括仰焊、立焊、平焊等几种焊接位置。焊接时焊条角度要随着各位置的变化而不断地变化,每条焊道焊接前,必须把前一层焊道的焊渣及飞溅物清理干净,焊道接头处打磨平整,避免缺陷产生。
5.2.2.1 焊道分布三层三道。
5.2.2.2 焊接工艺参数,见表125。
表 125 焊接工艺参数
焊接层数 |
焊条直径
mm |
焊接电流
A |
打底焊 |
2.5 |
60~80 |
填充焊 |
2.5 |
70~90 |
盖面焊 |
2.5 |
60~80 |
5.2.2.3 打底焊
a) 从起点引燃电弧,稍预热后,向上顶送焊条,待坡口的根部熔化形成熔孔后,稍退出焊条,用短弧作小幅度锯齿形横向摆动,沿顺时针方向继续焊接。
b) 现场由于管子厚度不同,所需热量也不一样,打底焊接应使电弧的热量偏向大管(或联箱),当焊条横向摆到大管(或联箱)一侧时,应稍做停顿,以保证大管(或联箱)坡口边缘熔合良好,防止大管(或联箱)一侧产生未熔合现象。
c) 在仰焊位置焊接时,焊条向坡口里面顶送得比平焊位置深些,平焊位置顶送焊条,应比立焊浅些,防止熔化金属由于重力作用而造成背面焊缝过高而产生焊瘤。
e) 焊完一根焊条时,将电弧住坡口的下方回带约10 mm,焊条慢慢提高熄弧,避免弧坑出现缩孔。
f) 焊接接头可采用热接或冷接法(详参见《管-管焊接及操作工艺》部分)。
5.2.2.4 填充焊:填充焊的焊条角度与焊接步骤与打底焊相同,但焊条摆动幅度比打底层大些。填充的焊道要薄些,两侧坡口均要填满,大管子(或联箱)要比小管子坡口一侧宽出约2 mm,使焊道形成一个斜面,保证盖面焊道焊后能够圆滑过渡。
5.2.2.5 盖面焊:焊接顺序、焊条角度、送条方法均与填充层相同。但摆幅要均匀,在两侧稍停留,保证焊缝焊脚均匀,无咬边。
5.3 垂直固定仰焊
5.3.1 装配与定位焊装配要求,见表126。
表 126 装配与定位焊装配要求
坡口角度
0 |
装配间隙
mm |
错边
mm |
错边量
mm |
45±5 |
2.5~3.2 |
0~1 |
<1 |
5.3.2 焊接及操作工艺要点
垂直固定仰焊接过程中要尽量压低电弧,利用电弧吹力将熔化金属吹入熔池。
5.3.2.1 焊道分布三层四道。
5.3.2.2 焊接工艺参数,见表127。
表 127 焊接工艺参数
焊接层数 |
焊条直径
mm |
焊接电流
A |
打底焊 |
2.5 |
60~80 |
填充焊 |
2.5 |
70~90 |
盖面焊 |
2.5 |
60~80 |
5.3.2.3 打底焊:必须保证焊根熔合好,背面焊道成形美观。
a)在左侧定位焊缝上引燃电弧,稍预热后,将焊条向背部下压,形成熔孔后,开始小幅度锯齿形横向摆动,转入正常焊接。打底时的焊条角度如图166所示。

图 166 仰焊打底时的焊条角度
b)焊接时,电弧尽可能短,电弧在两侧稍停留,必须看到坡口根部熔合在一起后才能继续往前焊。电弧稍偏向大管(或联箱),以免烧穿小管(或插座)。
c)焊缝接头和收弧操作要点同前,注意必须在熔池前面引弧,回焊一段后再转入正常焊接。
d)焊最后一段封闭焊缝前,最好将已焊好的焊缝两端磨成斜坡,以便接头。
5.3.2.4 填充焊
a) 填充焊的焊条角度,操作要领与打底相同,但焊条摆幅和焊接速度都稍大些,必须保证焊道两侧熔合好,表面整齐。
b) 开始填充前,先清理打底焊道上的飞溅物和熔渣,并将局部凸出的焊道磨平。
5.3.2.5 盖面焊
a) 盖面层有两条焊道,先焊上面的焊道,后焊下面的焊道。盖面焊时的焊条角度如图167所示。
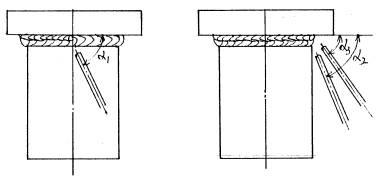
图 167 盖面时的焊条角度
a1=70°~80° a=70°~80° a=70°~80°
b) 焊上面的盖面焊道时,要保证管子上焊脚达到8 mm~10 mm,焊道上沿与上面的焊道合好,并将斜面补平,防止表面出现环形凹槽或凸起。
c) 盖面焊道的焊接顺序、摆动方法,收弧和焊缝接头的方法与打底焊相同。
5.4 焊后热处理 参见《管-管对接工艺》焊后热处理部分。
5.5 焊后检验
5.5.1 外观检验
5.5.1.1 用眼睛或5倍左右放大镜检验焊缝正面和背面缺陷性质和数量,并用测量工具测定缺陷位置和尺寸。
5.5.1.2 焊缝尺寸只测最大值和最小值,不取平均值。单面焊的背面焊缝宽度可不测定。
5.5.1.3 外观检查必须符合以下要求。
a) 焊脚凹凸度≤1.5 mm,管座焊脚为δ<3 mm~5 mm。
b) 焊缝外表不得有裂纹、气孔、未熔合和焊瘤。其它允许缺陷见下表128。
表 128
缺陷名称 |
允许的最大尺寸 |
咬边 |
深度≤0.5 mm,两侧咬边总长度≤20%周长 |
未焊透 |
深度≤15%,且≤1.5 mm总长度≤10%周长 |
背面凹坑 |
深度≤25%,且≤1 mm,总长度≤10%周长 |
5.5.2 金相检验
5.5.2.1 没有裂纹和未熔合缺陷。
5.5.2.2 未焊透深度≤15%的壁厚。
5.5.2.3 不允许有直径大于1.5 mm的气孔或夹渣,允许有一个直径在0.5 mm~1.5 mm的气孔或夹渣或允许有三个以下直径小于0.5 mm的气孔或夹渣。
5.5.2.4 其它标准参考《管—管焊接工艺》焊后检查部分。
6 钨极氩弧焊
6.1 我厂常用机具及材料
6.1.1 电焊机:ZX7—315ST
6.1.2 焊枪:PQ—85/150型冷式氩弧焊枪。
6.1.3 氩气减压流量计:AT—15/30。
6.1.4 钨棒:铈钨棒:φ2.5 mm。
6.1.5 焊丝:我厂常用氩弧焊丝,见表129。
表 129
序号 |
焊丝 |
材料 |
1 |
TIG—J50 |
20G |
2 |
TIG—R31 |
12Cr1MoV或12CrMoV |
3 |
TIG—R40 |
10CrMo910 |
6.1.6 氩气:纯度:≥99.99%。
6.2 焊前准备
6.2.1 坡口型式:V型坡口(60°~70°)
6.2.2 对口间隙:2.0 mm ~2.5 mm。
6.2.3 钝边:0 mm~1 mm。
6.2.4 清理:管子坡口和距坡口小于10 mm~15 mm范围内的内外侧及焊丝均应清理干净,露出金属光泽。
6.2.5 防风雨:焊接场所应严格防风、防雨措施,管内防止穿堂风进入。
6.2.6 不得强行对口,并在点焊时和焊接中均不可碰撞和撬动管道,以免开裂。
6.2.7 严禁采取加热管道使其伸长进行对口的方法。
6.3 焊接及操作工艺
6.3.1 引弧:为了提高焊接质量,多采用引弧器引弧或引弧板引弧,根据生产实际,一般在坡口面磨擦引弧,绝不允许在管壁上引弧。
6.3.2 定位焊
6.3.2.1 定位焊缝:定位焊是焊缝的一部分,必须焊牢,不允许有缺陷。
6.3.2.2 定位焊缝必须按正式的焊接工艺施焊,如果正式焊缝要求预热、缓冷,则定位焊前也要预热,焊后要缓冷。
6.3.2.3 定位焊缝不能太高,以免焊接到定位焊缝处接头困难,如果碰到这种情况,最好将定位焊缝磨低些,两端磨成斜坡,以便焊接时接头容易。
6.3.2.4 如果定位焊缝上发现裂纹、气孔等缺陷,应将其打磨掉重焊,绝不允许用重熔的办法修补。
6.3.3 焊接和接头
6.3.3.1 打底焊
a) 打底焊缝应一气呵成。
b) 打底层应有一定厚度:δ≤10 mm的管子,其厚度≥2 mm~3 mm;δ>10 mm的管子,其厚度≥4 mm。
6.3.3.2 焊接操作工艺要点
a) 焊接时要掌握好焊枪角度,送到位置,力求送丝均匀,才能保证焊缝成形美观,焊第二层时,应注意不得将打底层焊道烧穿,防止焊道下凹或背面剧烈氧化。
b) 接头质量控制:
接头处理要有斜坡,不能有死角;
重新引弧的位置在原弧坑后面,使焊缝重叠5 mm~10 mm,重叠处一般不加或只加少量焊丝。
熔池要穿到接头的根部,以确保接头处熔透。
6.3.4 填丝
6.3.4.1 焊丝紧贴坡口与钝边一起熔入,即将焊丝弯成弧形,紧贴在坡口间隙处,焊接电弧熔化坡口钝边的同时也熔化焊丝。
6.3.4.2 填丝注意事项:
a) 必须等坡口两侧熔化后才能填丝,以免造成熔合不良。
b) 填丝时,焊丝应与工件表面夹角成15°左右。
c) 填丝要均匀,快慢适当。过快焊缝余量大;过慢则焊缝下凹和咬边。焊丝端头应始终处在保护区内。
d) 对口间隙大于焊丝直径时,焊丝应跟随电弧同步横向摆动,不得扰动氩气保护层,以防空气侵入。
e) 操作过程中,如果不慎使钨极与焊丝相碰,发生瞬间短路,将产生很大的飞溅和烟雾;会造成焊缝污染和夹钨。这时应立即停止焊接,用砂轮磨掉被污染处,直至磨出金属光泽。被污染的钨极,应在别处重新引弧熔化掉污染端部,或重新磨尖后,方可继续焊接。
f) 撤回焊丝时,不要让焊丝端头撤出保证区,以免焊丝端被氧化,在下次进入熔池时,造成氧化物夹渣或产生熔孔。
6.3.5 收弧
收弧不当,会影响焊缝质量,使弧坑过深或产生弧坑裂纹,甚至造成返修。
6.3.5.1 最后收弧时,一般多采用稍拉长电弧,重叠焊缝10 mm~20 mm,在重叠部分不加或少加焊丝。速度要快。
6.3.5.2 停弧后,氩气开关应延时10 s左右再关闭,防止金属在高温下继续氧化。
6.4 焊后热处理及焊后检查
参考“管—管”部分。
注:高压管道壁厚≤6 mm,应采用全氩弧焊接,壁厚>6 mm的高压管道应采用氩弧焊打底(≥3 mm),手工电弧焊填充和盖面(工艺参考前面内容)。
7 补焊与堆焊工艺
7.1 补焊工艺
范围:大径管、三通、插座等。
7.1.1 焊前准备
7.1.1.1 查出缺陷位置,把缺陷彻底消除,尤其是裂纹缺陷,必要时要打止裂孔。
7.1.1.2 缺陷位置不好时,可用火焊把缺陷割掉,或用与之相匹配的焊条把缺陷清除掉。
7.1.1.3 该预热的除要求预热外,还应在对称部位加热500 ℃±100 ℃,以减少应力。
7.1.1.4 其它焊前准备可参考《管—管焊接工艺》的焊前准备部分。
7.1.2 焊接及操作工艺
7.1.2.1 如果管子内有水或汽的介质,可先用酸性焊条打底直至无介质泄漏,再用与母材相匹配的焊条进行焊接。
7.1.2.2 焊接时层间温度≥150 ℃。
7.1.2.3 多层多道焊时,每层厚度≤3 mm,同时避免接头过多重叠。
7.1.2.4 填充时,焊缝表面显微凹陷以减少应力。
7.1.2.5 其它工艺参考《管—管焊接工艺》部分。
7.1.3 焊后热处理及焊后检验,参考《管—管焊接工艺》焊后热处理和焊后检验部分。
注:同一位置补焊不多于三次,否则更换管子;
若条件允许建议用氩弧焊打底。
7.2 堆焊工艺范围:各种大小轴、门口、叶片等。
7.2.1 焊前准备
7.2.1.1 把工件放于水平位置(轴建议立放且底部不受力,但要固定)。
7.2.1.2 用火焊烤或汽油等把待焊部位的油、锈等杂质彻底清除,置至露出金属光泽,必要时用砂轮机打磨或进行机械加工车光,尤其是堆焊部分有丝扣时,更应如此。
7.2.1.3 焊条选择:碳钢工件建议选用J507;合金工件选用D547M。或D802(焊条应按要求烘干、保温)。
7.2.1.4 预热温度:150 ℃~300 ℃。
7.2.1.5 其它焊前准备参见通用准备。
7.2.2 焊接及操作工艺
7.2.2.1 焊接电流及比正常焊时小10%~20%。
7.2.2.2 堆焊焊大件时,应对称焊接,以减少应力及变形。
7.2.2.3 焊接过程中采用短弧焊接(弧长小于焊丝直径)。
7.2.2.4 多层多道焊时,每层厚度≤3 mm,道与道间距为:重叠1/3~1/2。
7.2.2.5 堆焊门口时,应先从小圆开始施焊。
7.2.2.6 堆焊切削余量≥3 mm。
7.2.2.7 焊后应进行良好的保温,以防止产生裂纹等缺陷。
7.2.2.8 其它工艺及焊后检查
参见《管—管焊接及操作工艺》工艺及焊后检查部分。
8 几种不常用焊接工艺要点
8.1 不锈钢焊接工艺要点
8.1.1 我公司常用材质为:1Cr18Ni9Ti,焊材:A132或A137。
8.1.2 不锈钢焊条适用于具有药皮的手工电弧焊焊接用铬及铬镍耐腐蚀钢和耐热钢焊条。这类焊条通常用于含于铬量大于4%,含镍量小于50%的耐腐蚀钢或耐热钢的焊接。
8.1.3 铬不锈钢可焊性较差。铬13型不锈钢焊后硬化性较大,容易产生裂纹,若采用同类型的铬不锈钢焊条A202焊接,则必须进行300 ℃以上的预热和焊后700 ℃左右回火缓冷处理。若焊件不进行焊后热处理,则应采用A107或A207等焊接。
8.1.4 铬17型不锈钢:焊接性比铬13型不锈钢好,焊条也可采用A102、A107、A207等焊接,焊后可不进行热处理。
8.1.5 铬18型不锈钢为铁素体组织,焊接时过热会促使晶粒长大,可用A402或A407等焊条焊接,焊后可不进行热处理。
8.1.6 奥氏体不锈钢在施焊时,受到重复加热,会析出碳化物,从而降低钢的腐蚀性和机械性能,因此应根据工作温度及介质种类妥善选择焊条(我公司通常选用A132焊条)。
8.1.7 为防止由加热而产生晶间腐蚀,焊接电流不宜过大,一般比碳钢焊条应低10%~20%左右,同时电弧不要过长,层间快冷,以单道焊为宜。
8.1.8 我公司常用不锈钢材质与焊条选择,见表130。
表 130
钢号 |
焊材 |
备注 |
0Cr13、1 Cr13 |
A107、A202、A207 |
焊口径300 ℃以上预热回火720 ℃—740 ℃,缓冷 |
1Cr18Ni9Ti、0Cr18Ni9Ti |
A132、A137 |
一般不热处理,但层间温度不宜过高。 |
8.1.9 重要部件建议用钨极氩弧焊打底或焊接。
8.2 铸铁焊接工艺要点
8.2.1 由于铸铁的含碳量高,组织不均匀,塑性低,属于可焊性不良的材料。在焊接过程中极易产生火口、裂纹和气孔等缺陷。为防止产生缺陷,在施焊工艺上建议采用如下措施:
8.2.2 焊接处必须清理干净,不得有砂眼、油泥、水、锈等污物存在。修补裂纹时,应开70°~90°坡口,必要时,打止裂孔以免裂纹扩展。
8.2.3 预热焊时,先将焊件预热至500 ℃~600 ℃左右,选择适当电流,可连续焊接,在焊接过程中始终保持预热温度,焊后趁红热状态覆盖以石棉粉或其它保温材料,达到缓慢冷却,有利于石墨析出。
8.2.4 冷焊时,尽量用小电流,短弧、窄焊道,短焊段,每面焊缝长度15 mm~20 mm,并施行焊后锤击焊缝隙以松驰应力,防止开裂,待温度下降于60 ℃以下时再焊下一道。收弧时,注意填满弧坑,以防焊口裂纹。
8.3 铜及铜合金焊接工艺要点
8.3.1 铜及铜合金焊条种类很多,除了用紫铜电焊条焊接紫铜外,目前采用较多的是用青铜焊条来焊接各种铜及铜合金、铜与钢等。由于铜及铜合金具有良好的耐蚀性,优良的耐磨性,因此也常用于堆焊轴承等承受金属间磨擦、磨损的零件和耐腐蚀件。
8.3.2 铜及铜合金的焊接较钢的焊接困难,易产生金属氧化,金属元素蒸发、气孔、裂缝以及变形等缺陷。
8.3.3 焊前应将氧化物、油脂及其他污染清除干净。由于铜的热膨胀系数大,因此在凝固时发生较大的收缩应力,造成裂缝和变形,所以装配间隙要宽,坡口角度要大,还可以采用多点暂时固定焊。铜和铜合金的导热性特别高,必须预热并用较大的电流焊接。铜及铜合金结晶后晶粒容易粗大,为了保证焊接质量,施焊后应用手锤对焊缝进行锤击,以消除应力及使晶粒细化。
8.3.4 重要部件建议采用氩弧焊焊接。
8.4 铝及铝合金焊接工艺要点
8.4.1 铝及铝合金焊条主要用于焊接钝铝、铝锰、铸铝及部分铝镁合金的焊接和补焊。焊接铝及对接头性能要求不高的铝合金用钝铝焊条。焊缝有较高的抗裂性能用铝硅焊条,铝硅焊条有较好的耐蚀性,可用于铝锰合金、钝铝及其他铝合金的焊接。
8.4.2 电弧焊接铝及铝合金时,易出现金属氧化、元素烧损、气孔、裂纹等缺陷。因焊条的药皮是盐基型,电弧稳定性差,飞溅大,极易吸潮,使用前应经150 ℃烘(1~2)小时。施焊前焊件坡口的油污、氧化物等杂质应用碱蚀法消除干净。焊后在焊缝留下的残渣必须用蒸气或热水洗刷干净,以免产生腐蚀。板厚小于6 mm可不开坡口,6 mm~12 mm开V型坡口,大于12 mm开X型坡口,夹角60°~70°。焊接时采用直流电源,焊条接正极。可根据工件厚度加热到200 ℃~300 ℃后施焊。焊时,不作摆动,以提高焊接速度。更换焊条必须快速进行,焊接时应采用垫板。
8.4.3 重要部件建议用钨极氩弧焊。
9 气焊及气割工艺
9.1 气焊工艺
9.1.1 焊丝及焊剂
9.1.1.1 气焊用的焊丝起填充作用,与熔化的母材一起组成焊缝金属。因此,根据工件的化学化分选用成份、类型相同的焊丝,见表131。
表 131
序号 |
型 号 |
化学成份(%) |
C |
Mn |
Si |
Cr |
Ni |
Mo |
V |
其它 |
SIP不大于 |
1 |
H08 |
≤
0.10 |
0.30~
0.55 |
≤
0.30 |
≤
0.20 |
≤
0.30 |
|
|
|
0.040 |
0.040 |
2 |
H08A |
≤
0.10 |
0.30~
0.55 |
≤
0.30 |
≤
0.20 |
≤
0.30 |
|
|
Cu≤
0.20 |
0.030 |
0.030 |
3 |
H08MnA |
≤
0.10 |
0.80~
1.10 |
≤
0.70 |
≤
0.20 |
≤
0.30 |
|
|
|
0.040 |
0.040 |
4 |
H08CrMoVA |
≤
0.10 |
0.40~
0.70 |
0.15~
0.35 |
0.80~
1.10 |
≤
0.30 |
0.40~
0.60 |
|
|
0.030 |
0.030 |
5 |
H08CrMoA |
≤
0.10 |
0.40~
0.70 |
0.15~
0.35 |
1.00~
1.30 |
≤
0.30 |
0.50~
0.70 |
0.15~
0.35 |
|
0.030 |
0.030 |
6 |
hs401 |
3.0~
4.2 |
0.30~
0.80 |
2.8~
3.6 |
|
|
|
|
|
0.08 |
0.5 |
7 |
hs402 |
3.8~
4.2 |
0.30~
0.80 |
3.0~
3.6 |
|
|
|
|
|
0.05 |
0.5 |
9.1.1.2 常用气焊焊剂,见表132。
表 132
牌号 |
名称 |
用途 |
CJ101(气剂101) |
不锈钢及耐热钢 |
不锈钢耐热钢气焊 |
CJ201(气剂201) |
铸铁气焊焊剂 |
铸铁气焊 |
CJ301(气剂301) |
铜气焊剂 |
铜及铝合金气焊 |
CJ401(气剂401) |
铝气焊剂 |
铝及铝合金气焊 |
9.1.2 坡口型式:一般I型或V型坡口,见图168。
(a) (b)
图 168 坡口型式
(a—I型 b—V型)
9.1.3 气焊火焰的选择焰。
9.1.3.1 中性焰
a) 中性焰是氧乙焰混合比为1.1~2.2。
b) 特征为亮白色的焰心端部有淡白色火焰闪动,时隐时现。
c) 内焰区气体为CO和H2,无过量氧,也没有游离碳呈暗紫色。
d) 内焰并非中性,而是具有一定的还原性。
e) 焰心外2 mm~4 mm处温度最高。达3 150 ℃左右,气焊时焰心离开工件表面2 mm~4 mm热效率最高。
f ) 适用于低碳钢、中碳钢、低合金钢、不锈钢、紫铜、锡青铜、铝及铝合金、铜、镁合金和灰铸等焊接。
9.1.3.2 碳化焰
a) 氧乙炔混合小于1.1。
b) 特征是内焰呈淡白色。
c) 有较强的还原作用,也有一定的渗碳作用。
d) 适用于高碳钢、铸铁、高速钢、硬质合金、铝青铜等的焊接。
9.1.3.3 氧化焰
a)氧乙炔的混合比大于1.2。
b)特征是焰心端部无淡白色火焰闪动,内焰与外焰分不清。
c)氧化焰有过量的氧,具有氧化性。
d)适用于黄铜、锰黄铜、镀锌铁皮等的焊接。
9.1.4 气焊工艺参数
9.1.4.1 火焰能率
火焰能率是由焊炬型号及焊嘴号的大小决定的,在实际生产中,可根据工件厚度选择焊炬型号和焊嘴号。气焊时,对于一种型号的焊炬及焊嘴号,还可以在一定范围内调节火焰的大小。气焊紫铜等导热性产量的工件,应选用大的焊炬型号和焊嘴号。水平焊位置所焊时,应选用小的焊炬型号和焊嘴号。见表133。
表133
型号 |
工件厚度
mm |
工作压力
MPa |
C2H2工作压力
MPa |
可换焊嘴
个 |
H01—2 |
0.5~2 |
0.1~0.25 |
0.001~0.10 |
5 |
H01—6 |
2~6 |
0.2~0.4 |
0.001~0.10 |
5 |
H01—12 |
6~12 |
0.4~0.7 |
0.001~0.10 |
5 |
H01—20 |
12~20 |
0.6~0.8 |
0.001~0.10 |
5 |
9.1.4.2 焊丝直径
焊丝直径是根据工件厚度选择的,选择焊丝直径时,可参考表134。
表 134
工件厚度
mm |
1~2 |
2~3 |
3~5 |
2~10 |
10~15 |
>15 |
焊丝直径
mm |
1~2 |
2 |
2~3 |
3~4 |
4~6 |
6~8 |
9.1.4.3 焊嘴倾斜角度
a) 焊嘴倾角是指焊嘴与工件平面间略<90°的夹角,火焰热量散失小,工件加热快,温度高。
b) 焊嘴倾角大小可根据工件厚度、火焰大小、工件加热和工件材质等确定。
c) 气焊低碳钢时,左向焊焊嘴倾角约30°~50°,右向焊嘴倾角约50°~60°,开始焊接时,为了加热快,焊嘴倾角要大,可80°~90°,焊接结束时,为了填满焊坑,避免烧穿,焊嘴颂角要减小。
d) 气焊导热性强的紫铜时,焊嘴倾角为60°~80°。
e) 气焊熔点低的铝及铝合金时,焊嘴倾角要小。
9.2 气割工艺
9.2.1 气割工艺参数
9.2.1.1 预热火焰能率:火焰能率太大,会使切口上缘产生连续珠状钢粒,甚至熔化成圆角,并增多工件表面粘附的熔渣,火焰能率主要决定于割炬和割嘴的大小,割炬大小与割嘴号,可根据工件厚度参考表135。
表 135
型号 |
割嘴
号码 |
割嘴
形式 |
切割底碳钢厚度mm |
切割氧孔径mm |
气体压力
MPa |
气体消耗量
t/m2 |
|
|
|
氧气 |
乙炔 |
氧气 |
乙炔 |
G01—30 |
1
2
3 |
环形 |
3~10
10~20
20~30 |
0.7
0.9
1.1 |
0.2
0.25
0.3 |
0.001~0.1 |
13.3
23.3
26.7 |
3.5
4.0
5.2 |
|
G01—100 |
1
2
3 |
梅花形 |
10~25
25~50
50~100 |
1.0
1.3
1.6 |
0.3
0.4
0.5 |
0.001~0.1 |
36.7~45
58.2~71.7
91.7~121.7 |
5.8~6.7
7.7~8.3
9.2~10 |
|
G01—300 |
1
2
3
4 |
梅花形 |
100~150
150~200 |
1.8
2.2 |
0.5
0.65 |
0.001~0.1 |
150~180
183~233 |
11.3~11
13.3~18.3 |
|
环形 |
200~250
250~300 |
2.6
3.0 |
0.8
1.0 |
|
242~300
167~433 |
19.2~20
20.8~26.7 |
9.1.1.2 氧气压力:氧气压力主要根据工作厚度确定(参表135),切割氧压力太小,气割过程缓慢,在切口表面形成粘渣,甚至无法割穿。切割氧压太大,不但浪费氧气,而且使切口变宽,切口表面粗糙。
9.1.1.3 切割速度:切割速度合适时,火焰和熔渣等接近于垂直的方向喷向工件的底面,切口质量好,速度太慢时,会使切口上缘熔化,切口过宽。速度太快时,后拖量过大,甚至切割不透。正常的后拖量约为板厚的10%~15%。
9.1.1.4 割嘴离工件表面的距离:预热火焰焰心一般应离开工件表面2 mm~4 mm。
9.1.1.5 割嘴的倾斜角:一般,割嘴应垂直于工件表面。直线切割时,当工件厚度小于20 mm时,割嘴可向切割方向反向后倾20°~30°。工件厚度大于20 mm的直线切割以及曲线切割时,割嘴均应垂直于工件面。
附录 A
(资料性附录)
焊接工艺卡
表A.1 小直径碳钢疏水管(吊焊)
焊接方法 |
钨极氩弧焊手工电焊盖面 |
母材 |
钢号:20g(δ=3.5 mm~6.0 mm) |
坡口形式 |
|
焊前准备 |
1.焊丝清理干净
2.坡口及两侧各为10 mm~15 mm的内外壁彻底清理
3.坡口角度及装配尺寸见左图
4.错口值≤10%δ且≤1 mm
5.工作环境及工作位置良好
6.不允许强行对口 |
焊接材料 |
钨极氩弧焊:TIGJ50(ψ2.4) 焊条 J4303 或J5515(直径3.2) |
预热制度 |
预热温度:150 ℃~250 ℃或不预热 |
焊后处理
制 度 |
可不热处理 |
焊接规范
参 数 |
焊接电流:60A~90A(极性:电焊反接,氩弧焊正接) 焊接电流 100A~110A(直流反接)
焊接电压:16V~25V
焊接层数:两层两道 |
操作技术 |
焊接位置:全方位 焊条角度:随位置变化而变化
焊工分布:对称焊接 接头重叠:10 mm~15 mm
焊接方式:短弧焊接 打底面形状:微凹
摆动方向:横向微动 接头分布:尽量避免过多重复
层间厚度:≤3 mm 焊接完成后氩气延时10s左右。 |
焊接工艺卡
表A.2 小直径高压合金钢管(横焊)
焊接方法 |
钨极氩弧焊打底电焊盖面 |
母材 |
钢号:12Cr1MoV(δ=3 mm~6 mm) |
坡口形式 |
|
焊前准备 |
1.焊丝清理干净
2.坡口及两侧各为10 mm~15 mm的内外壁彻底清理
3.坡口角度及装配尺寸见左图
4.错口值≤10%δ且≤1 mm
5.工作环境及工作位置良好
6.不允许强行对口 |
焊接材料 |
焊丝TIG-R31(φ2.4) 焊条 R317(直径3.2 ) |
预热制度 |
预热温度: |
焊后处理
制 度 |
|
焊接规范
参 数 |
焊接电流:60A~90A(直流正接) 氩气流量:Q=6121/min
焊接电压:10V~12V 钨极直径: φ2.5
焊接电流:105A~125A(直流反接) 喷嘴至工作距离: ≤10 mm |
操作技术 |
焊接位置:横向焊接 焊条角度:随位置变化而变化
焊工分布:对称焊接 打底面形状:微凹
摆动参数:不摆动 接头分布:尽量避免过多重复
层间厚度:≤3 mm 焊接完成后氩气延时10S左右
接头重叠:5 mm~10 mm |
焊接工艺卡
表A3大直径合金管(吊焊)
焊接方法 |
手工电弧焊或氩弧焊 |
母材 |
钢号:20g(δ=3.5 mm~6.0 mm) |
坡口形式 |
|
焊前准备 |
1.焊条烘干(300 ℃~400 ℃)
2.坡口及两侧各为10 mm~5 mm的内外壁彻底清理
3.坡口角度及装配尺寸见左图
4.错口值≤10%δ且≤1 mm
5.工作环境及工作位置良好
6.不允许强行对口 |
焊接材料 |
钨极氩弧焊(打底):TIG—R31(ψ2.4)
手工电弧焊(填充及盖面):R317(ψ3.2或ψ4) |
预热制度 |
预热温度:250 ℃~350 ℃ |
焊后处理
制 度 |
正火:960 ℃~980 ℃
回火:740 ℃~760 ℃ |
焊接规范
参 数 |
焊接电流:90A~110A(氩弧焊直流正接)
105A~125A(ψ3.2直流反接)
150A~180A(ψ4直流反接)
焊接电压:16V~25V |
操作技术 |
焊接位置:全方位 打底厚度:≥2 mm
焊接层数:多层多道 焊条角度:随位置变化而变化
焊工分布:对称焊接 接头重叠:10 mm~15 mm
焊接方式:短弧焊接 填充面形状:微凹
摆动方向:横向 接头分布:尽量避免过多重复
层间厚度:≤3 mm 焊缝收尾:回焊将弧坑填满 |
焊接工艺卡
表A.4主蒸汽温度插座(垂直固定俯焊)
焊接方法 |
手工电弧焊或氩弧焊 |
母材 |
钢号:12Cr1MoV(δ=4 mm~8 mm)+12Cr1MoV(δ≥12 mm) |
坡口形式 |
|
焊前准备 |
1.焊条烘干(300 ℃~400 ℃)
2.坡口及两侧各为10 mm~15 mm的内外壁彻底清理
3.坡口角度及装配尺寸见左图
4.错口值≤10%δ且≤1 mm
5.工作环境及工作位置良好
6.不允许强行对口 |
焊接材料 |
钨极氩弧焊:TIG—R31(ψ2.4)
手工电弧焊:R317(ψ3.2) |
预热制度 |
预热温度: 250 ℃~350 ℃
层间温度:≥250 ℃ |
焊后处理制度 |
正火:960 ℃~980 ℃
回火:740 ℃~760 ℃ |
焊接规范
参 数 |
焊接电流:90 A~110 A(氩弧焊直流正接)
105 A~125 A(电焊直流反接)
焊接电压:16 V~25 V |
操作技术 |
焊接位置:垂直俯焊 打底厚度:1/3~1/2
焊接层数:多层多道 焊条角度:随位置变化而变化
焊工分布:对称焊接 接头重叠:10 mm~15 mm
焊接方式:短弧焊接 填充面形状:微凹
摆动方向:不摆动 接头分布:尽量避免过多重复
层间厚度:≤3 mm 焊缝收尾:回焊将弧坑填满 |
|
|
|
|
|